When selecting motor bearings based on load and speed requirements, several factors should be taken into consideration to ensure optimal performance and longevity. Here are key factors to consider:
Radial Load and Axial Load: Undertake a meticulous engineering analysis to precisely quantify the varying magnitudes and directions of both radial and axial loads throughout the entire operational spectrum. Consider transient load conditions, dynamic load fluctuations, and potential shock loads. Utilize advanced simulation tools to model load distributions under different scenarios and ensure the selected bearings can withstand the full spectrum of expected loading conditions.
Dynamic Load Rating (C): Conduct an exhaustive examination of the dynamic load rating (C) in the context of the application's dynamic requirements. Account for factors such as load sharing among multiple bearings, dynamic variations in load distribution, and the effects of rapid acceleration and deceleration. Employ advanced fatigue analysis techniques to predict bearing life accurately, factoring in dynamic load variations and potential load spikes.
Static Load Rating (Co): Scrutinize static load conditions in minute detail, considering all conceivable scenarios where the application may experience prolonged stationary periods or static loads. Undertake stress analysis to determine the static load limits of the bearings, ensuring that the static load rating (Co) provides a substantial safety margin to prevent any risk of permanent deformation under static conditions.
Speed Ratings: Conduct an in-depth speed analysis that goes beyond mere rotational speed considerations. Explore transient speed variations, the impact of rapid acceleration and deceleration, and the effects of vibration on bearing performance. Utilize computational fluid dynamics (CFD) simulations to assess the dynamic fluid film characteristics at varying speeds, ensuring that the selected bearings not only meet but exceed the specified speed ratings under all operational scenarios.
Bearing Type: Undertake an extensive comparative analysis of different bearing types, considering not only load-bearing capabilities but also nuanced characteristics such as preload adjustments, internal clearances, and potential skewing effects in roller bearings. Employ finite element analysis (FEA) to model the behavior of different bearing types under diverse load and speed conditions, ensuring that the selected type aligns perfectly with the application's requirements.
Precision Requirements: Embark on a precision engineering journey to meet or exceed the stringent precision requirements of the application. Dive into the intricacies of runout, eccentricity, and dynamic runout analysis. Utilize advanced metrology techniques and precision measurement tools to ensure that the selected bearings provide the necessary levels of precision demanded by the application, leaving no room for deviation.
Temperature Conditions: Conduct an exhaustive thermal analysis, considering every conceivable factor influencing temperature conditions, from ambient temperature variations to the heat generated during operation. Implement thermal imaging and thermographic analysis to map temperature gradients across bearings. Explore the thermal expansion characteristics of different bearing materials and lubricants, ensuring that the selected bearings can operate within precise temperature constraints.
Lubrication: Undertake an all-encompassing lubrication strategy that considers not only the type of lubricant but also its viscosity, oil film thickness, and the impact of operating temperatures on lubricant properties. Employ tribology simulations to model the fluid film behavior under varying loads and speeds. Develop a lubrication schedule that optimizes bearing performance and extends operational life, leaving no room for uncertainty in the lubrication strategy.
Mounting Arrangement: Embark on a precision mounting endeavor, utilizing advanced alignment tools and techniques to achieve unparalleled precision during installation. Employ laser alignment systems, shimming methods, and precision measurement instruments to eliminate any potential misalignment issues. Conduct comprehensive structural analysis to assess the impact of mounting arrangements on bearing alignment, ensuring a flawless installation process.
Single Row Deep Groove Ball Bearings
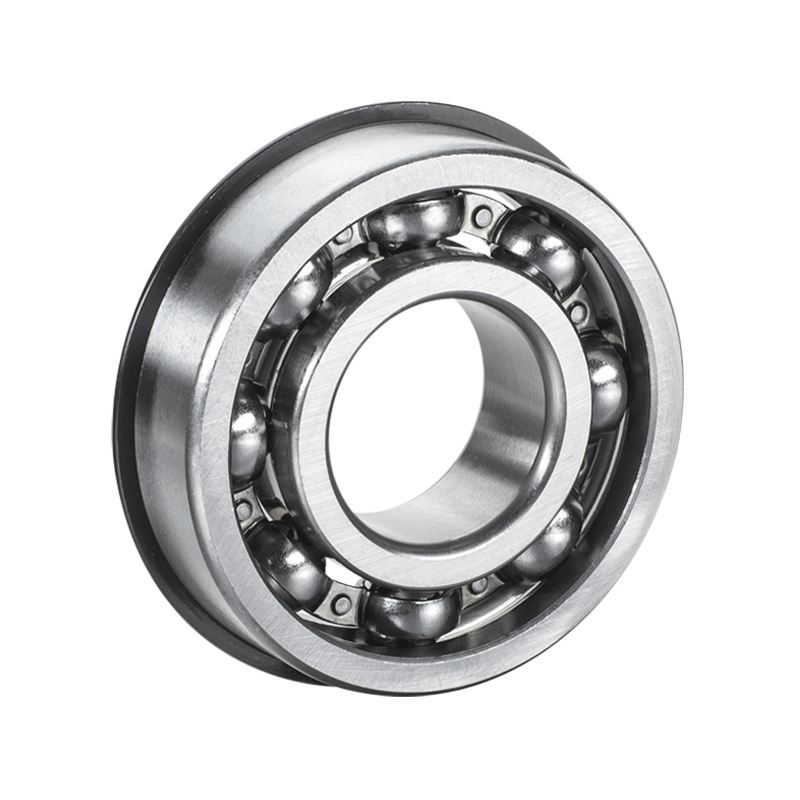
Single Row Deep Groove Ball Bearings
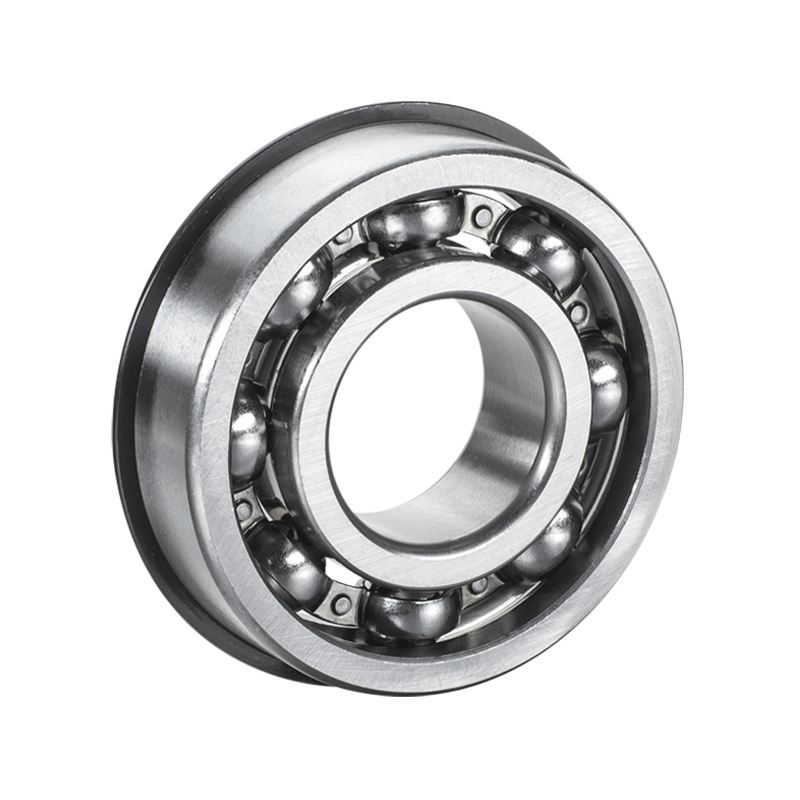