Cleanliness: Thoroughly clean all surfaces involved in the bearing mounting process to an immaculate standard. Utilize industry-standard cleaning agents and methods to ensure the removal of even the most stubborn contaminants. Employ practices such as solvent flushing, ultrasonic cleaning, or vapor degreasing to achieve pristine conditions. A clean mounting surface minimizes the risk of abrasive particles or debris entering the bearing assembly, which could cause premature wear or damage.
Inspect Components: Conduct a meticulous inspection of every component related to the bearing installation. Utilize magnification tools and non-destructive testing techniques such as dye penetrant inspection or magnetic particle testing to detect even the slightest surface defects or anomalies. Pay close attention to critical areas such as bearing raceways, rolling elements, and cage structures. Any signs of wear, pitting, cracking, or corrosion should prompt immediate replacement to ensure the integrity and reliability of the bearing assembly.
Proper Handling: Handle bearings with the utmost care and precision throughout the entire installation process. Employ cleanroom protocols or wear lint-free gloves to prevent contamination from skin oils or dirt particles. Utilize specialized handling equipment such as bearing lifters, vacuum suction devices, or magnetic handlers to minimize the risk of physical damage during transportation and installation. Avoid any sudden impacts, drops, or shocks that could result in microstructural alterations or stress concentrations within the bearing components.
Alignment: Attain precise shaft and housing alignment with a degree of accuracy that exceeds industry standards. Employ advanced alignment techniques such as laser interferometry or computerized alignment systems to achieve sub-micron level alignment tolerances. Conduct dynamic alignment analysis to account for operational loads, thermal expansion effects, and dynamic forces that may affect the long-term stability of the bearing arrangement. Implement corrective measures such as shim adjustments, thermal compensation, or flexure analysis to mitigate any misalignment-induced stresses or distortions that could compromise bearing performance.
Lubrication: Apply lubricants with a level of precision that optimizes bearing performance under the most demanding operating conditions. Utilize advanced lubrication techniques such as hydrodynamic lubrication analysis or boundary film modeling to determine the most suitable lubricant type, viscosity, and application method. Implement automated lubrication systems or centralized lubrication units to ensure consistent lubricant delivery and distribution throughout the bearing assembly. Monitor lubricant quality and condition using real-time condition monitoring systems or lubricant analysis techniques to detect potential contamination, degradation, or loss of lubricating properties.
Temperature Control: Maintain strict temperature control measures throughout the bearing installation process to prevent thermal distortions, dimensional changes, or metallurgical alterations that could compromise bearing integrity. Implement precision heating or cooling systems such as induction heaters, resistance heaters, or liquid nitrogen immersion baths to achieve uniform temperature profiles and minimize thermal gradients. Monitor temperature fluctuations in real-time using thermocouples, infrared sensors, or thermal imaging cameras to ensure compliance with specified temperature limits during heating, cooling, and post-installation stabilization phases.
Paired Single Row Tapered Roller Bearings
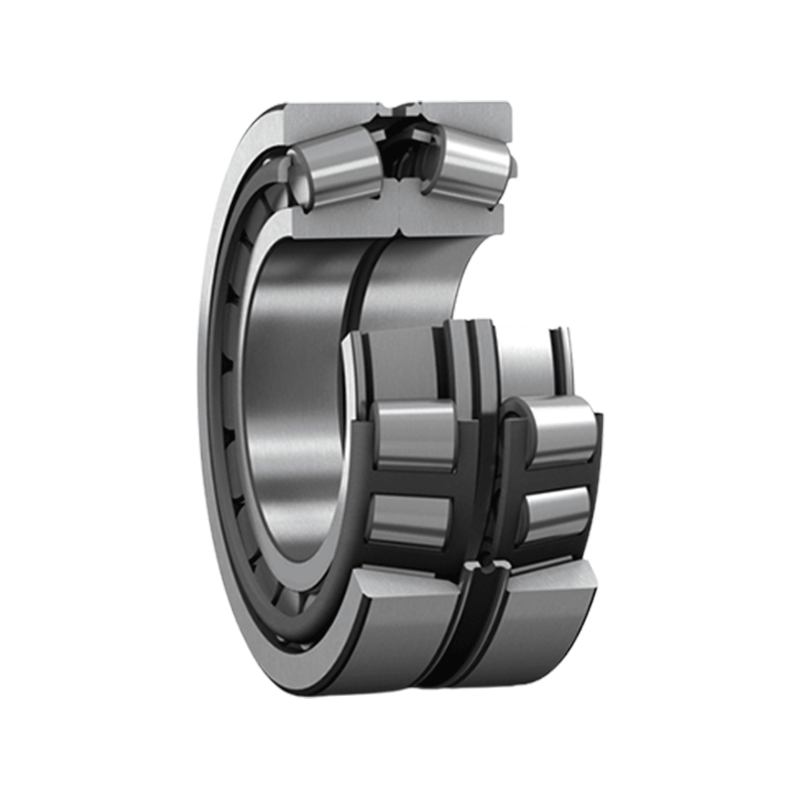