Parallel Alignment: Achieving precise parallel alignment of shafts supporting screw compressor bearings is paramount for several reasons. When shafts are not parallel, bearings experience uneven loading, leading to localized stress concentrations. This can result in accelerated wear of bearing surfaces and premature failure. Misalignment can induce shaft deflection, causing vibration and noise, further exacerbating wear and reducing operational efficiency. Proper parallel alignment is achieved through meticulous measurement and adjustment procedures, such as using dial indicators or laser alignment tools. During installation and maintenance, technicians must carefully align the shafts to ensure uniform distribution of loads across the bearings, thereby maximizing their service life and minimizing downtime.
Angular Alignment: Angular misalignment occurs when the shaft axes intersect at an angle rather than being perfectly aligned. This misalignment introduces radial and axial forces on the bearings, leading to increased friction and stress. As a result, bearings experience uneven loading, which can cause localized overheating and accelerated wear. Angular misalignment can induce shaft bending, exacerbating vibration and noise issues. To address angular misalignment, precise measurement techniques, such as the double-check method or reverse indicator method, are employed to detect and correct deviations from the desired alignment. By ensuring angular alignment conformity, technicians can mitigate bearing wear and enhance the overall reliability and efficiency of screw compressors.
Axial Alignment: Proper axial alignment of screw compressor bearings is crucial to prevent excessive thrust loading, which can lead to premature bearing failure. Axial misalignment occurs when the shafts are not positioned symmetrically along their axis, resulting in unequal distribution of axial forces on the bearings. This can cause thrust bearings to experience overload conditions, leading to fatigue and eventual failure. To achieve optimal axial alignment, technicians employ precision measurement techniques, such as feeler gauges or dial indicators, to ensure symmetrical positioning of shafts relative to their axis. Additionally, alignment shims or spacers may be utilized to fine-tune axial alignment during installation or maintenance. By maintaining proper axial alignment, operators can mitigate the risk of thrust bearing failure and ensure the long-term reliability of screw compressor systems.
Alignment Tools: Precision alignment tools play a crucial role in achieving and maintaining proper alignment of screw compressor bearings. These tools enable technicians to accurately measure and adjust shaft positions, ensuring alignment conformity within specified tolerances. Laser alignment systems, for example, project laser beams onto target surfaces, allowing technicians to visualize and adjust shaft positions in real-time. Similarly, optical alignment tools utilize telescopic sights or digital cameras to align shafts with high precision. Advanced alignment software provides real-time feedback and analysis, enabling technicians to make informed adjustments to achieve optimal alignment conditions. By leveraging these alignment tools, operators can streamline alignment procedures, minimize human error, and maximize the performance and reliability of screw compressor bearings.
Screw Compressor Thrust Spherical Roller Bearings
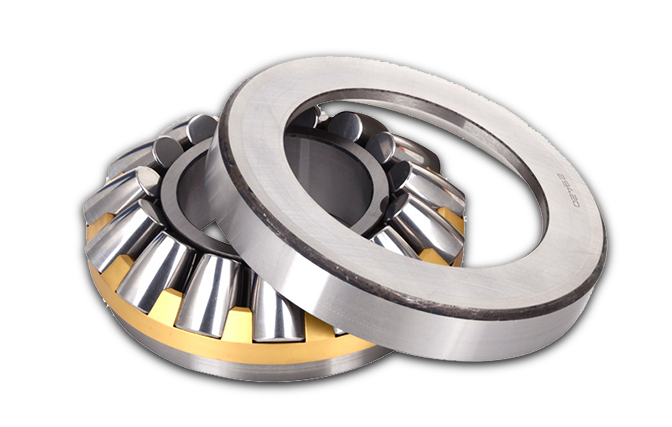
DHK thrust self-aligning roller bearings are available in three different configurations based on different dimensions and cage designs. Small and medium size self-aligning roller bearings can be solid copper cage (suffix MB) or stamped steel cage (suffix J); The standard structure for large self-aligning roller bearings is a solid copper cage (suffix MB).