Environmental factors like temperature and humidity can significantly impact the performance of rolling mill bearings in several ways:
Temperature Effects on Lubrication: Temperature fluctuations exert a profound influence on the performance of lubricants within rolling mill bearings. Elevated temperatures induce thermal degradation in lubricants, causing them to break down and lose viscosity. This viscosity reduction diminishes the lubricant's ability to form a robust film between bearing surfaces, leading to increased friction and wear. Consequently, bearings subjected to high temperatures are more susceptible to premature failure and decreased operational efficiency. Conversely, low temperatures cause lubricants to thicken, impeding their flow characteristics and impairing their ability to reach critical areas within the bearing assembly. To mitigate these temperature-induced challenges, meticulous selection of lubricants with suitable viscosity grades and thermal stability is imperative.
Temperature Effects on Lubrication: Temperature fluctuations exert a profound influence on the performance of lubricants within rolling mill bearings. Elevated temperatures induce thermal degradation in lubricants, causing them to break down and lose viscosity. This viscosity reduction diminishes the lubricant's ability to form a robust film between bearing surfaces, leading to increased friction and wear. Consequently, bearings subjected to high temperatures are more susceptible to premature failure and decreased operational efficiency. Conversely, low temperatures cause lubricants to thicken, impeding their flow characteristics and impairing their ability to reach critical areas within the bearing assembly. To mitigate these temperature-induced challenges, meticulous selection of lubricants with suitable viscosity grades and thermal stability is imperative.
Thermal Expansion and Bearing Clearance: The thermal expansion and contraction of bearing components in response to temperature variations can significantly impact bearing clearances and fits, thereby influencing operational performance. As temperatures rise, bearing components expand, potentially reducing internal clearances and altering the distribution of loads within the bearing assembly. Conversely, lower temperatures induce contraction, leading to increased clearances and potential misalignment issues. Engineers must carefully consider these thermal effects during bearing design and installation processes to maintain proper clearances and ensure optimal operational conditions. Employing advanced materials with favorable thermal expansion coefficients and implementing precise clearance settings are critical strategies for mitigating temperature-induced dimensional changes and preserving bearing integrity.
Humidity-Induced Corrosion and Contamination: High humidity levels in the operating environment of rolling mills pose significant challenges for bearing performance due to the propensity for moisture-related corrosion and contamination. Moisture ingress can compromise the integrity of lubricants, leading to oxidation, rust formation, and lubricant breakdown. Moisture-laden environments promote the growth of microorganisms and accelerate corrosion of bearing surfaces, further exacerbating wear and reducing bearing lifespan. To combat these deleterious effects, comprehensive sealing solutions must be implemented to prevent moisture infiltration into bearing cavities. Regular maintenance practices, including lubricant analysis and seal inspections, are essential for detecting and mitigating humidity-induced issues before they escalate and cause catastrophic bearing failure.
Seal Integrity and Environmental Protection: The effectiveness of seals and shields in preventing environmental contaminants from entering bearing cavities is paramount for ensuring long-term reliability and performance. However, exposure to extreme temperature and humidity conditions can compromise seal integrity over time, rendering them susceptible to leakage and failure. To mitigate these risks, we employ advanced sealing technologies, including labyrinth seals, lip seals, and contact seals, designed to withstand harsh environmental conditions and provide robust protection against moisture and contaminants. Proactive maintenance measures, such as regular seal inspections and replacement intervals, are critical for preserving seal integrity and preventing costly downtime associated with bearing failure.
Series 248&249-Spherical Roller Bearings
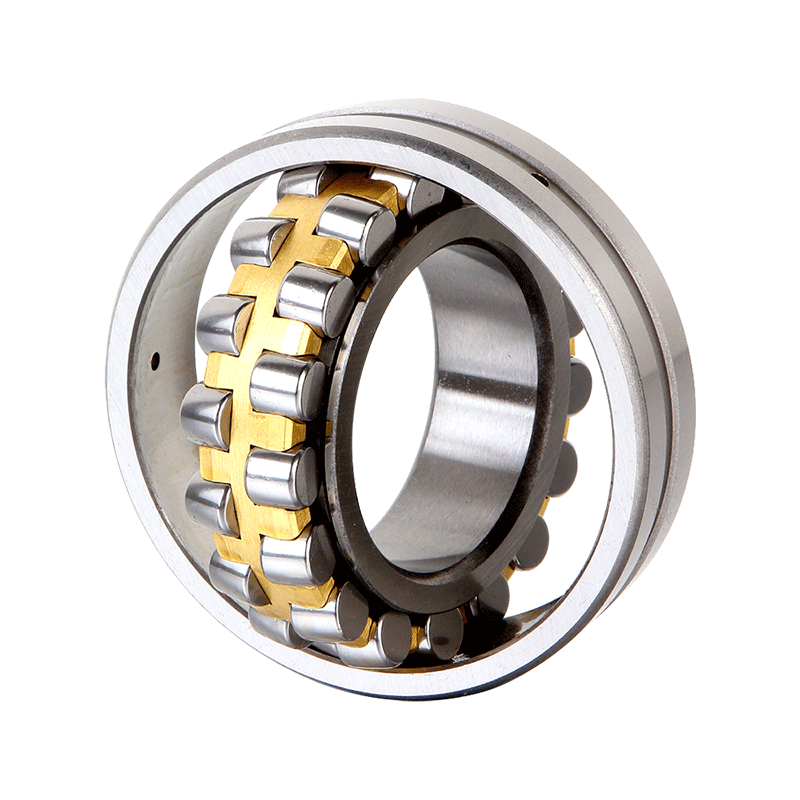
Series 248&249-Spherical Roller Bearings
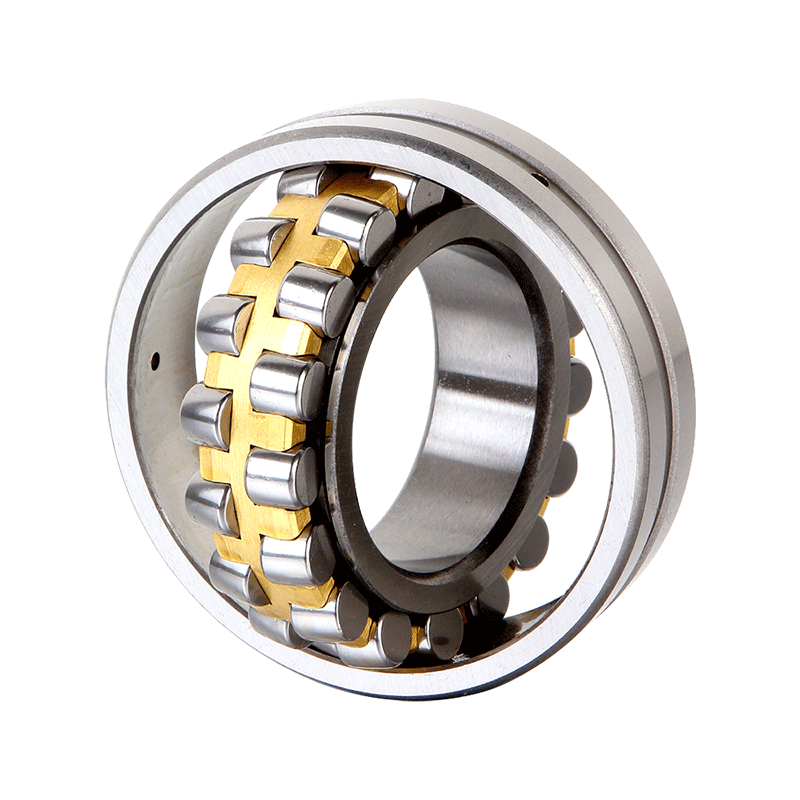