Using improper or damaged rolling mill bearings can have significant consequences in terms of safety and performance:
Increased risk of machinery failure: The ramifications of bearing failure in rolling mills can be profound. These bearings are the linchpin of the operation, tasked with enduring immense loads, high speeds, and harsh environmental conditions. When bearings are improperly selected or damaged, they become vulnerable points in the system, unable to cope with the demands placed upon them. The consequences of failure range from minor disruptions to catastrophic breakdowns, resulting in costly repairs, extended downtime, and lost production. Beyond the immediate financial impact, there's the potential for reputational damage and lost business opportunities if customers perceive the mill as unreliable or unsafe.
Reduced equipment reliability: Reliability is the cornerstone of any successful manufacturing operation, and rolling mills are no exception. However, when bearings are compromised, reliability goes out the window. Operators are left playing a high-stakes game of chance, never knowing when the next bearing failure will occur and bring production to a grinding halt. This uncertainty erodes trust in the equipment and undermines the mill's ability to meet delivery deadlines, fulfill customer orders, and maintain consistent output levels. As a result, the entire supply chain may suffer, with downstream partners experiencing delays and disruptions that ripple through the marketplace.
Safety hazards: Bearing failures aren't just inconvenient—they're downright dangerous. In a rolling mill environment, where heavy machinery operates in close proximity to human workers, safety is paramount. When bearings fail, they can unleash a cascade of events that pose serious risks to personnel and property. Flying debris, uncontrolled movements, and sudden equipment stoppages are just a few of the hazards that operators may encounter. The consequences can be severe, ranging from minor injuries to fatalities, not to mention the potential for costly damage to equipment and facilities.
Decreased product quality: Rolling mills are tasked with producing precision-engineered components to exacting specifications. Any deviation from these standards can have far-reaching consequences for product quality and customer satisfaction. When bearings are compromised, they introduce unwanted variables into the manufacturing process, such as vibration, noise, and dimensional inaccuracies. These imperfections may not be immediately apparent but can manifest themselves in the form of rejected parts, rework, and customer complaints down the line. The integrity of the mill's products and brand reputation hang in the balance, making it imperative to address bearing issues promptly and decisively to maintain quality standards and competitive advantage.
Energy inefficiency: Inefficient bearings can exact a heavy toll on energy consumption and operational costs. When bearings are improperly selected or worn, they introduce unnecessary friction and resistance into the system, requiring higher energy inputs to maintain the same level of performance. This increased energy demand not only drives up utility bills but also contributes to carbon emissions and environmental impact. The excess heat generated by friction can accelerate bearing wear and exacerbate the problem, creating a vicious cycle of energy inefficiency and equipment degradation. Implementing energy-saving measures, such as lubrication optimization and bearing upgrades, can help mitigate these effects and improve the overall sustainability of rolling mill operations.
Double Row Tapered Roller Bearings
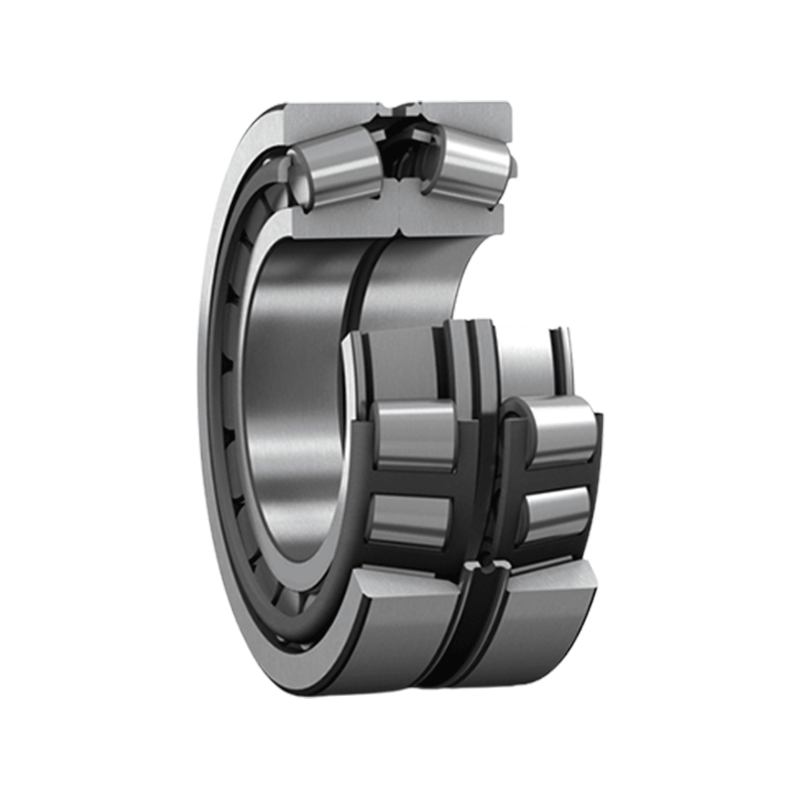
Double Row Tapered Roller Bearings
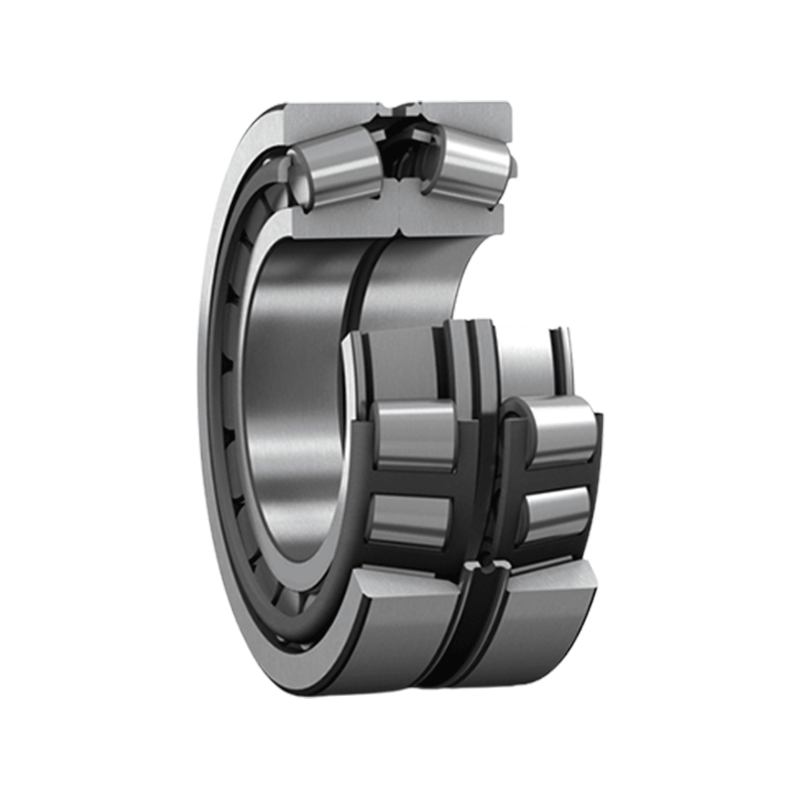