Heat generation in spherical roller bearings can have significant implications for their operational efficiency and overall performance. Excessive heat can lead to increased friction, accelerated wear, and ultimately, premature failure of the bearing. Here's how heat generation affects operational efficiency and some measures to mitigate it:
1.Friction and Wear: Heat is often a byproduct of friction within the bearing. Increased friction results in higher temperatures, causing accelerated wear on the rolling elements and raceways. This can lead to a reduction in bearing life and increased maintenance requirements.
2.Material Properties: High temperatures can affect the material properties of the bearing components, such as the steel used for the rollers and raceways. Elevated temperatures may lead to a reduction in hardness and overall strength, further compromising the bearing's ability to handle loads.
3.Lubrication Breakdown: Excessive heat can cause lubricants to break down or evaporate, leading to insufficient lubrication. Inadequate lubrication results in increased friction, wear, and the potential for metal-to-metal contact, all of which contribute to reduced operational efficiency.
4.Clearance Changes: Elevated temperatures can alter the internal clearance of the bearing. This can impact the distribution of loads and may result in misalignment, affecting the bearing's ability to handle radial and axial loads.
5.Seal and Cage Performance: High temperatures can affect the performance of seals and cages in spherical roller bearings. Seals may lose their effectiveness, allowing contaminants to enter the bearing, while cages may experience thermal deformation, affecting their ability to retain and guide the rolling elements.
Mitigation Measures:
1.Proper Lubrication: Conduct a thorough lubrication analysis, considering factors such as viscosity, base oil type, and additives tailored to the bearing's operating conditions.
Implement a centralized lubrication system with programmable controllers to ensure precise and timely lubricant delivery.
Establish a proactive lubricant management program, including scheduled oil changes and filtration systems to maintain optimal lubricant quality.
2.Cooling Systems: Employ advanced cooling techniques such as air-oil or water-oil cooling systems to efficiently dissipate heat from critical bearing components.
Integrate temperature sensors and thermal imaging technology to monitor real-time heat distribution and identify potential hotspots.
Perform computational fluid dynamics (CFD) simulations to design and optimize cooling systems for maximum heat dissipation.
3.Optimal Clearance: Conduct a detailed thermal analysis using finite element analysis (FEA) to precisely determine the thermal expansion characteristics of the bearing.
Explore advanced bearing designs, such as self-adjusting clearance mechanisms, to dynamically adapt to temperature fluctuations and maintain optimal clearance.
Utilize laser alignment tools and 3D metrology for precision mounting, ensuring consistent clearances during installation.
4.Material Selection: Collaborate with material scientists to customize bearing materials, considering factors such as alloy composition, heat treatment processes, and surface coatings.
Implement advanced surface engineering techniques, such as nitriding or ceramic coatings, to enhance the bearing's wear resistance and thermal stability.
Perform in-depth material testing, including hardness and fatigue testing, to validate the suitability of chosen materials for high-temperature applications.
5.Avoid Overloading: Employ sophisticated simulation software to model and analyze complex loading scenarios, considering dynamic forces, vibrations, and shock loads.
Implement load-sharing strategies using multiple bearings to distribute loads evenly and prevent localized overloading.
Utilize strain gauges and load cells for real-time monitoring of applied loads, enabling proactive adjustments to prevent overloading.
6.Proper Mounting and Alignment: Utilize laser interferometry for ultra-precise alignment, minimizing installation-induced stresses and ensuring optimal load distribution.
Implement vibration analysis tools during installation to detect any initial misalignments that may contribute to heat generation.
Establish comprehensive installation and alignment procedures, incorporating best practices from industry standards and bearing manufacturers' recommendations.
Series 213-Spherical Roller Bearings
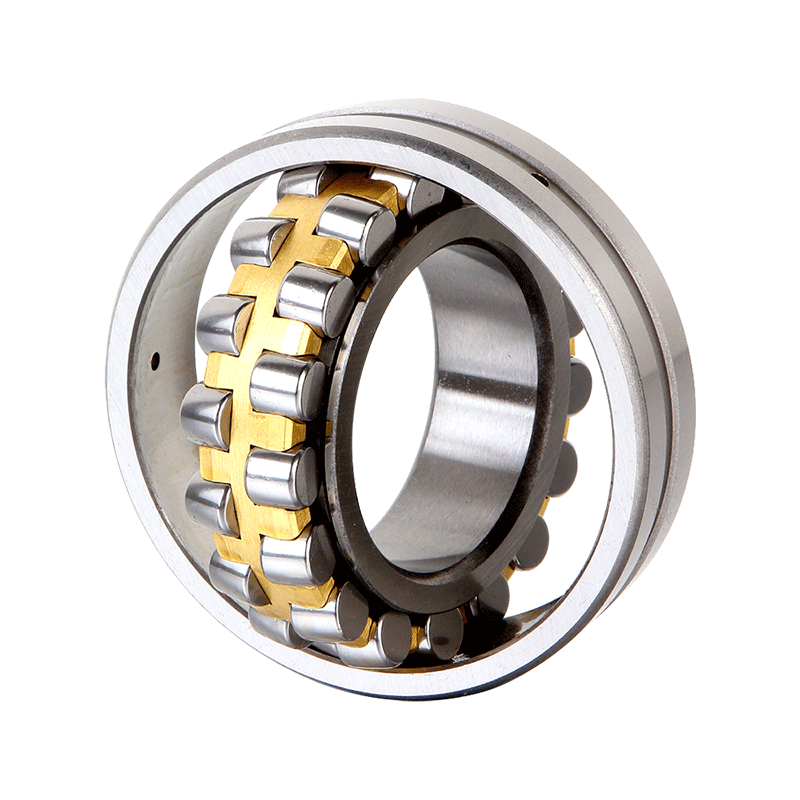
Series 213-Spherical Roller Bearings
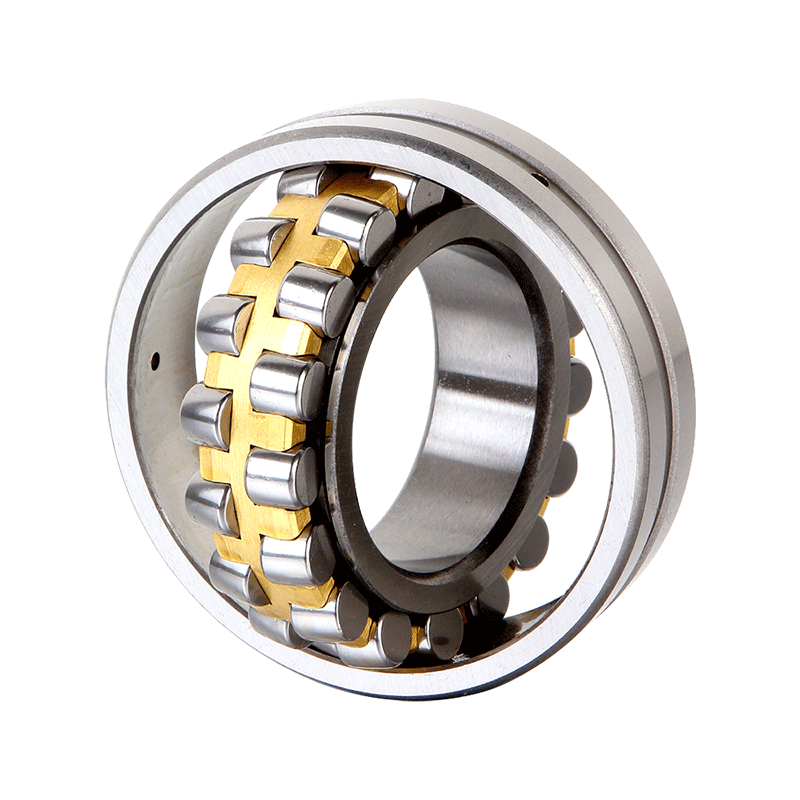