The actual service life of a rolling bearing depends on many factors - premature bearing failure can lead to costly plant downtime and sometimes even more serious consequences.
So, how do you maximise bearing life?
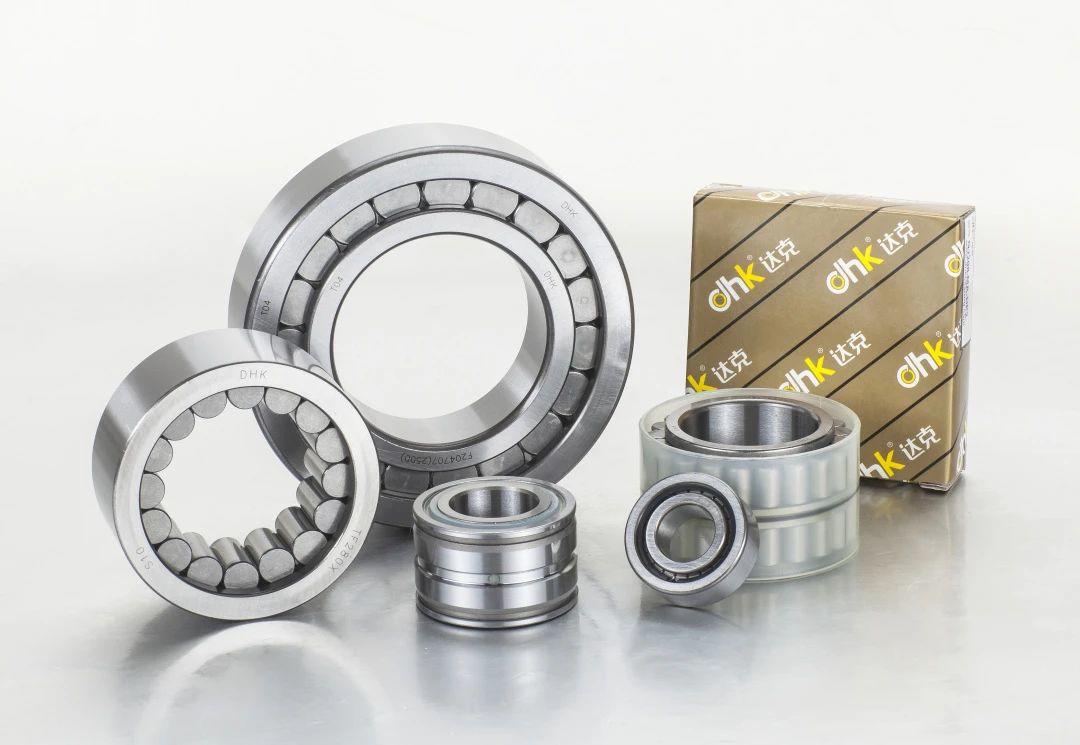
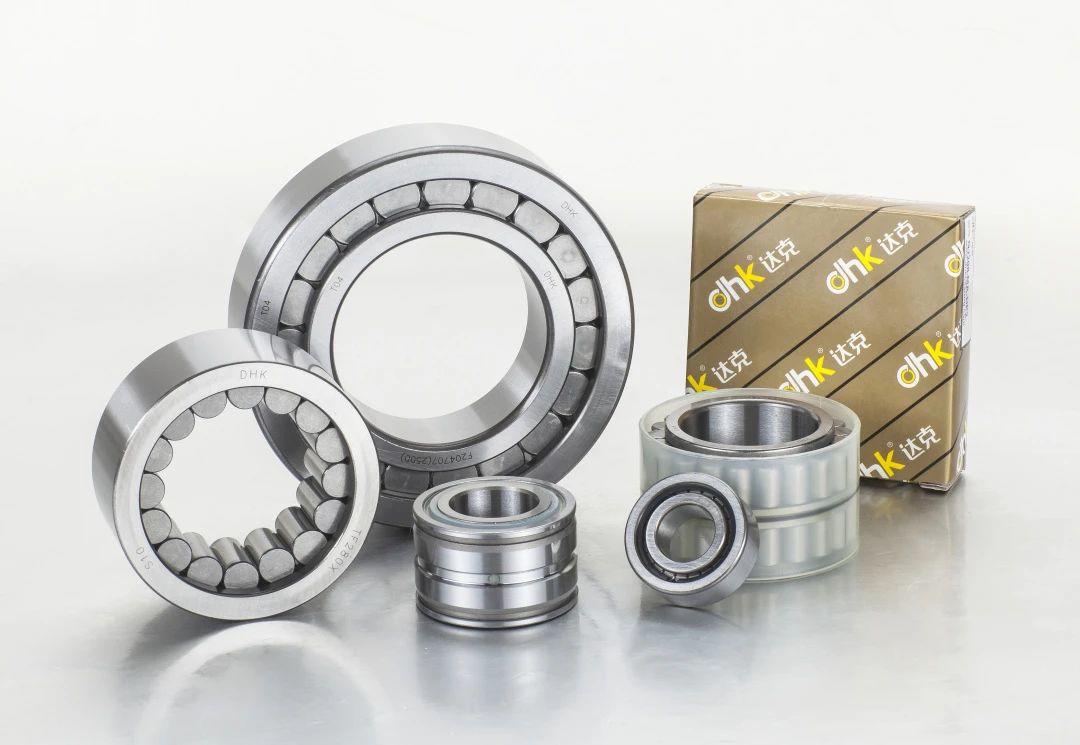
1. Correct bearing selection
Satisfactory bearing life starts with the right bearing selection. From the outset, bearing designers extend bearing life and equipment performance by selecting the right bearings for different applications. This process takes into account many factors, such as load, hardness, bearing life prediction, operating environment, etc.
2. Correct storage
In principle, all bearings should be stored in their original packaging until they are installed. They need to be left in a clean, moisture-free, relatively constant temperature environment.
Rolling bearings should be kept away from dust, water and corrosive chemicals. Shaking and vibration may permanently damage the mechanical properties of the bearings, so vibration must be avoided during handling and storage.
Basically, all bearings must be stored horizontally as some of the heavier bearings may deform due to their own weight after being stored vertically for a long period of time.
Pre-greased (or sealed) bearings require special care, as the density of the grease will change after a long period of storage. This can result in a certain degree of rotational noise when the bearing is first used. Therefore, the shelving time for such bearings should be controlled on a first-in, first-out basis.
3、Cleaning
Cleaning is very important for rolling bearings. The surface roughness of the rotating surfaces of the bearing rings and rolling elements is usually 1/10 μm. Such smooth surfaces are very sensitive to damage caused by contaminants.
The lubrication layer between the rotating surfaces is usually 0.2 to 1 μm. Particulate impurities larger than the lubricant particle size can be subjected to excessive rolling element crushing and local pressure in the bearing steel, which can eventually lead to permanent material fatigue.
In addition to this, dust particles in the external environment up to 10 μm in size can also cause damage to bearings. A clean and dust-free environment is therefore essential for the storage and mounting of bearings.
4. Thorough preparation before mounting
Bearings should be mounted and dismounted carefully using the appropriate tools. Industry experts estimate that 16% of premature bearing failure cases are due to incorrect mounting. For large installations (e.g. in production plants), it is usually necessary to mount under strictly controlled conditions, and suitable bearing mounting equipment can be used.
However, in maintenance or replacement work, the environment is diverse. Therefore, thorough preparation of the bearing installation is necessary to ensure maximum bearing life.
Firstly, the relevant documentation, such as drawings, maintenance manuals, product instructions etc., needs to be carefully studied. Next, all bearing components such as shafts, setting rings, caps, washers etc. must be kept absolutely clean and free from contamination. The condition of adjacent components should also be carefully checked.
5. Careful mounting and dismounting
Depending on the application and the size and type of bearing, the appropriate mounting method (mechanical or hydraulic) and tools have to be selected. Here are some basic principles of bearing mounting:
1. do not apply mounting forces on the rolling elements, this can easily lead to local overloading of the rolling elements and the contact surface of the seating ring, resulting in premature failure of the bearing.
2. Do not use any hard tools (e.g. hammers, drivers, etc.) to tap directly on the bearing surface, this can lead to fracture or shattering of the bearing rings.
Approximately 90% of rolling bearings are never removed from the equipment they are in, and usually only larger bearings are removed as a result of scheduled preventive maintenance procedures.
As with the mounting of a bearing, the dismantling of a bearing also requires careful preparation. During dismantling, ensure that adjacent components such as shafts and bushings are not damaged. It is important to select the appropriate method and tools depending on the type of bearing, its size and the application.
Designers should note that well-designed bearing positions can greatly simplify the mounting and dismounting of bearings and therefore reduce maintenance costs.
6. Correct and appropriate lubrication
Lubricants can isolate metal bearing surfaces (e.g. rolling elements, bearing rings and bearing covers) and therefore reduce friction, protect metal parts and combat contamination and impurities. A wide range of lubricants (including grease, oil and solids) are available for different operating conditions.
The correct choice of lubricant is important for extending the service life of bearings and equipment.
Due to the excessive rolling of the rolling parts, the bearing lubricant is subjected to prolonged mechanical stress and, in addition, the chemical properties of the lubricant are altered over time, especially in hot, wet or contaminated environments. All this leads to a gradual deterioration in the quality of the lubrication.
To ensure maximum service life, bearings should therefore be relubricated at regular intervals. The lubrication interval depends on the operating conditions, e.g. temperature, speed, environment, etc. Only in pre-lubricated or sealed bearings (also known as "lifetime lubricated" bearings) is the bearing life dependent on the lubricant life.
The lubricant must be stored correctly according to the manufacturer's instructions, taking particular care to keep the lubricant clean and free from contamination. Before each use, the quality of the lubricant should be carefully checked, as the use of old or contaminated lubricants may cause premature bearing failure.
7. Condition testing/maintenance
Generally speaking, rolling bearings are very reliable, although they have a limited life span. As with all other important components in a machine, they should be inspected and maintained regularly. The frequency of inspection and maintenance depends on the importance of the individual application and the operating conditions of the individual machine.
Due to the critical role of bearings, it is recommended that condition monitoring is included in their design phase. Important parameters of machine operation, such as vibrations and noise, can be continuously monitored and preventive measures can be taken before unpredictable and costly machine downtime.
8. Training - the basis for good practice
Practice makes perfect, but proper training is the basis for practice.
Major mistakes can be avoided if technicians have basic knowledge in handling bearings. Design and product development engineers can maximise equipment performance and minimise lifecycle costs by optimising bearing design.
Bearings are often an important component in pumps and other equipment, and although first-class quality bearings are very reliable, extra care must be taken to ensure they have the longest possible service life.
Correct storage, careful mounting and dismounting, adequate lubrication and relubrication, proper condition monitoring, timely maintenance and, finally, sound personnel training are all important for improving bearing life and plant performance.