Common failure modes or issues associated with Paired Single Row Tapered Roller Bearings include:
1.Fatigue Failure: Caused by repeated cyclic loading leading to the formation of cracks in the bearing components.
2.Surface Damage: Due to inadequate lubrication, contamination, or foreign particles causing abrasion or scoring on the bearing surfaces.
3.Misalignment: Excessive misalignment of shafts or housings can lead to uneven loading and premature wear on the bearing rollers and raceways.
4.Overloading: Applying loads beyond the rated capacity of the bearings can lead to plastic deformation or fracture of bearing components.
5.Corrosion: Exposure to corrosive environments can result in pitting, rusting, or chemical degradation of bearing surfaces, compromising their performance.
6.Improper Installation: Incorrect installation procedures, such as insufficient preload or misalignment during assembly, can lead to premature failure.
To prevent or address these issues, the following measures can be taken:
1.Proper Maintenance: Establish a centralized maintenance management system that integrates bearing maintenance schedules with overall equipment maintenance plans. This system should include automated reminders for lubrication, inspections, and replacements based on predetermined intervals or condition-based triggers.Utilize advanced maintenance techniques, such as predictive maintenance utilizing machine learning algorithms or remote monitoring technologies, to forecast bearing failure probabilities and optimize maintenance activities for maximum equipment uptime.
2.Correct Installation: Develop standardized installation procedures encompassing detailed step-by-step instructions, annotated diagrams, and video tutorials to cater to various skill levels among maintenance personnel. Conduct post-installation validation checks using precision measurement tools, such as dial indicators or laser alignment devices, to verify proper shaft alignment, bearing preload, and seating within the housing bore. Establish a cross-functional installation review process involving engineering, maintenance, and quality assurance teams to ensure alignment with engineering specifications and industry best practices.
3.Effective Lubrication: Conduct thorough lubrication audits to evaluate lubrication practices across the organization, identifying areas for improvement such as lubricant selection, application methods, and contamination control measures. Implement a centralized lubrication management system utilizing RFID tags or barcoding technology to track lubricant usage, replenishment schedules, and equipment compatibility, streamlining inventory management and reducing the risk of misapplication. Collaborate with lubricant suppliers and equipment manufacturers to conduct lubricant compatibility testing and optimize lubrication intervals based on real-world operating conditions and performance feedback.
4.Environmental Protection: Perform environmental risk assessments to identify potential sources of contamination, including airborne pollutants, water ingress points, and chemical exposure pathways, and develop targeted mitigation strategies tailored to each risk category. Invest in advanced sealing technologies, such as labyrinth seals or magnetic bearing protectors, capable of providing enhanced ingress protection without compromising bearing performance or heat dissipation characteristics. Implement stringent cleanliness protocols for maintenance activities, including the use of dedicated cleanrooms or filtered air enclosures for bearing storage, handling, and installation to minimize the introduction of contaminants into critical bearing surfaces.
5.Monitoring and Inspection: Deploy a comprehensive suite of condition monitoring sensors and instrumentation, including accelerometers, temperature probes, and oil analysis sensors, strategically positioned to capture real-time data on bearing health parameters and performance trends. Integrate condition monitoring data with enterprise asset management systems or cloud-based analytics platforms to facilitate centralized data aggregation, visualization, and trend analysis, enabling proactive decision-making and resource allocation based on predictive maintenance insights. Implement closed-loop feedback mechanisms linking condition monitoring data to maintenance action triggers, such as automated work order generation or equipment shutdown commands, to ensure timely intervention in response to emerging bearing degradation issues.
Paired Single Row Tapered Roller Bearings
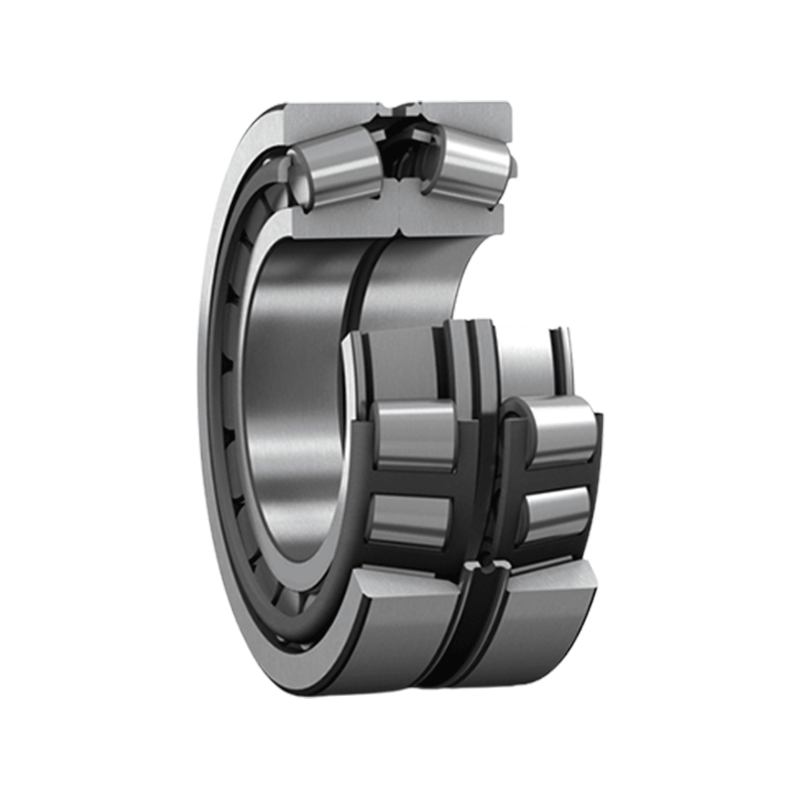
Paired Single Row Tapered Roller Bearings
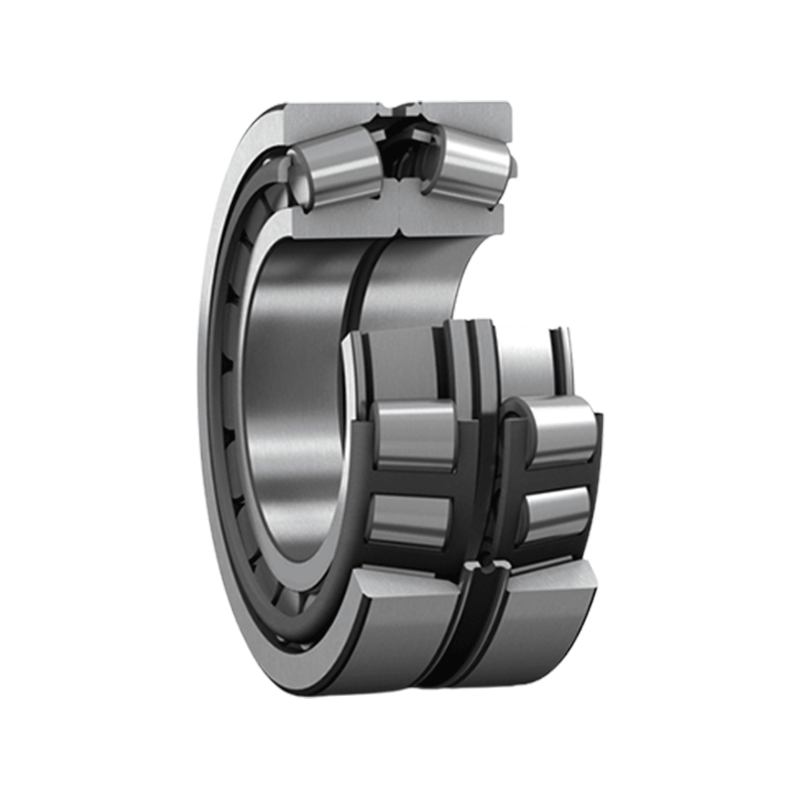