Bearing misalignment can significantly contribute to motor vibration, impacting both the performance and longevity of the bearings. Misalignment occurs when the centerlines of the rotating shaft and the bearing do not align properly. Here's an explanation of the role of bearing misalignment in motor vibration and how to address misalignment issues for optimized bearing performance:
Role of Bearing Misalignment in Motor Vibration:
1.Increased Load and Stress: Misalignment introduces additional forces and stresses on the bearing components, leading to uneven loading. This can result in increased wear and fatigue on the bearing elements.
2.Vibration Generation: Misalignment can cause irregular motion and forces within the bearing, leading to vibration. This vibration can propagate throughout the motor system, affecting overall performance and causing additional wear on components.
3.Temperature Rise: Misalignment contributes to increased friction and heat generation within the bearing. Elevated temperatures can accelerate wear and reduce the lubrication effectiveness, further exacerbating vibration issues.
4.Reduced Efficiency: Vibration and misalignment can decrease the overall efficiency of the motor, leading to energy losses and potentially impacting the performance of connected machinery.
Addressing Misalignment Issues for Optimized Bearing Performance:
1.Precision Installation: Employ state-of-the-art laser alignment tools, leveraging their high precision to the micrometer level. This ensures not just alignment but an exacting, surgical positioning of the motor shaft and bearings. Execute a meticulous installation process, leaving no room for error. This involves using precision instruments, like optical alignment devices, and adhering to a step-by-step installation procedure to achieve a level of precision that borders on the surgical.
2.Regular Alignment Checks: Integrate alignment checks into the very fabric of your maintenance schedule, making it as routine as changing the oil. Regularity is the key, ensuring that alignment is not just an event but an ongoing, relentless pursuit of perfection. Employ cutting-edge measurement techniques, such as 3D laser alignment, turning alignment checks into comprehensive, three-dimensional audits. This guarantees that even the slightest deviation from perfection doesn't escape detection.
3.Use of Laser Alignment Tools: Embrace laser alignment tools that not only provide precision but do so in real-time, offering a dynamic, live visualization of the alignment process. It's not just a tool; it's a window into the heart of your machinery. Leverage the wireless capabilities of modern laser alignment tools to transform the alignment process into a symphony of precision, where adjustments are made on the fly, and perfection is achieved without missing a beat.
4.Flexible Couplings: Select couplings that defy the conventional, those engineered with materials and designs that scoff at misalignment challenges. These aren't just couplings; they're resilient sentinels guarding against the forces of misalignment. Consider couplings that are not just passive components but active participants in the machinery ecosystem, equipped with diagnostics and monitoring capabilities. They don't just flex; they adapt and communicate, ensuring misalignment is detected before it becomes a problem.
5.Monitoring Systems: Immerse your machinery in a sensory network, a web of accelerometers strategically positioned to capture vibrations from every nook and cranny. It's not just monitoring; it's a symphony of data, a chorus of insights harmonizing to keep misalignment at bay. Integrate advanced analytics and machine learning algorithms, transforming your monitoring system into a proactive oracle. It doesn't just report; it predicts, enabling you to address misalignment issues before they dare to disrupt your operation.
Double Row Deep Groove Ball Bearings
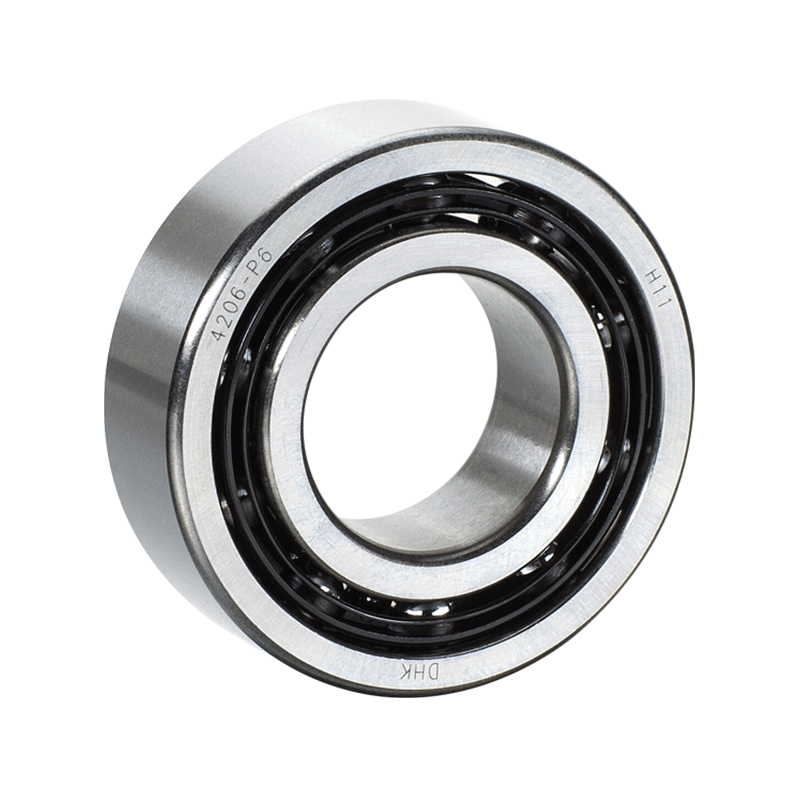
Double Row Deep Groove Ball Bearings
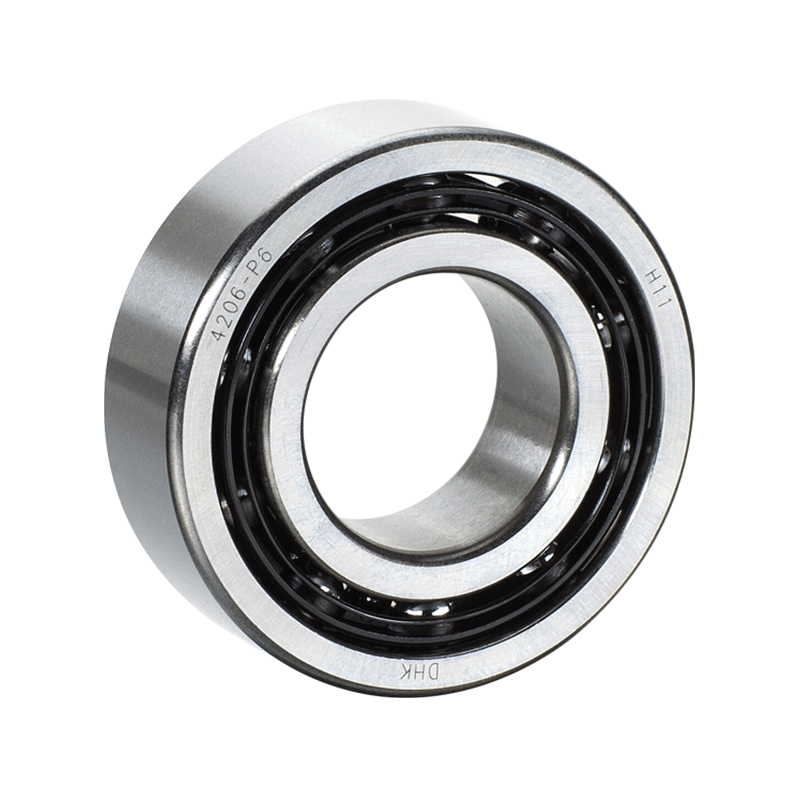