Roller bearing tolerances and fits play a crucial role in the assembly and operation of machinery by ensuring proper alignment, load distribution, and overall performance. Tolerances refer to the allowable variations in dimensions and geometry of bearing components, while fits define the relationship between the bearing and its mating parts, such as shafts and housings. Here's how roller bearing tolerances and fits influence machinery assembly and operation:
1.Alignment and Precision:
Tolerances and fits are instrumental in achieving precise alignment of bearing components. Tight tolerances ensure that the dimensions of the bearing and its mating parts conform closely to the intended design. This alignment is paramount for machinery performance, as deviations can lead to increased friction, wear, and reduced efficiency. Precision alignment is particularly critical in applications where tight tolerances are essential, such as high-precision machining and instrumentation.
2.Load Distribution:
Proper fits are fundamental to the even distribution of loads across the rolling elements and raceways. Bearings operating within the specified fits can distribute loads evenly, preventing localized stress concentrations. This uniform load distribution extends the bearing's service life by minimizing fatigue and wear, enhancing overall machinery reliability.
3.Interchangeability:
Standardized tolerances and fits facilitate interchangeability of bearings and components. This standardization simplifies maintenance and repair activities, as replacement parts can be readily sourced and installed without the need for extensive re-engineering or adjustments. Industries with high reliance on interchangeable components benefit significantly from adherence to established tolerance standards.
4.Vibration and Noise Reduction:
Tight fits can reduce internal clearances within bearings, minimizing axial and radial play. This reduction in play is effective in dampening vibrations generated during operation. In applications where noise and vibration control are paramount, such as precision metrology or aerospace systems, proper fits contribute to quieter and smoother machinery performance.
5.Temperature Management:
Roller bearings experience temperature variations during operation, which can affect their dimensions. Proper fits account for thermal expansion and contraction, maintaining clearances within acceptable limits. Bearings with incorrect fits may experience excessive temperature-related stresses, leading to premature failure. Maintaining proper clearances under varying temperatures is crucial for reliable machinery performance.
6.Preventing Excessive Play:
Bearings with appropriate fits prevent excessive axial or radial play. Excessive play can result in backlash, lost motion, or misalignment, impacting machinery precision and responsiveness. By controlling play within prescribed limits, fits contribute to stable and accurate machinery operation.
7.Load-Carrying Capacity:
The choice of fits can influence the effective load-carrying capacity of a bearing. For heavy-duty applications, where substantial loads or shocks are encountered, engineers may opt for looser fits to accommodate thermal expansion and provide a greater safety margin. Conversely, in precision applications, tighter fits may be favored to minimize micro-movements that can affect accuracy.
8.Assembly Ease:
Bearings designed with appropriate tolerances and fits simplify the assembly process. Properly selected fits reduce the likelihood of component damage during installation, ensuring that the bearing seats securely without excessive force. This ease of assembly streamlines production and minimizes the risk of costly errors during installation.
9.Lubrication and Sealing:
Tolerances and fits can significantly impact the effectiveness of lubrication and sealing systems. Tight fits enhance the retention of lubricants within the bearing, reducing the frequency of re-lubrication and enhancing bearing longevity. Additionally, proper fits contribute to the effectiveness of sealing arrangements, helping to exclude contaminants and maintain a clean, lubricated bearing environment.
10.Dynamic vs. Static Loads:
Roller bearings are often subjected to both dynamic loads (resulting from rotational motion) and static loads (non-rotational forces). The chosen fits should strike a balance between accommodating these loads while preserving precision and alignment. Proper selection ensures that the bearing remains responsive to both static and dynamic loading conditions, maintaining machinery efficiency and accuracy.
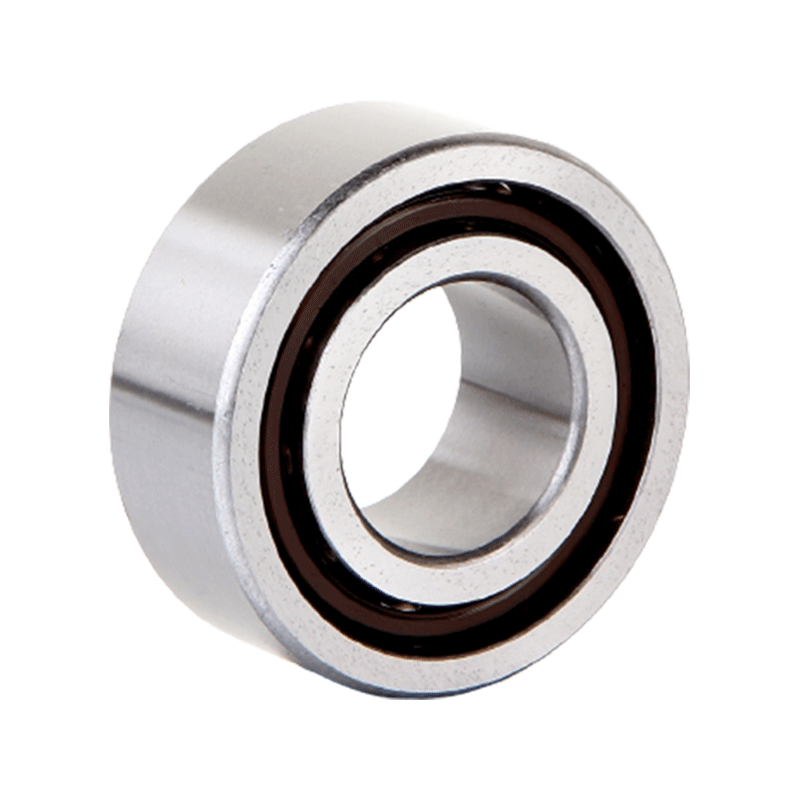
32 and 33 type double row angular contact ball bearings, feature a filling slot in one face and contact angle of 35 . These bearings must be mounted in such a way the large thrust force acts towards the raceway without the filling slot.