Challenges associated with screw compressor bearings can impact the performance, reliability, and efficiency of the compressor system. Here are some of these challenges and potential ways to address them:
1.High Load and Pressure:
Challenge: Screw compressors often operate in demanding industrial settings with high loads and pressures, which can subject bearings to significant stress and wear.
Solution: To address this challenge, it is crucial to select bearings specifically designed for high-load applications. Bearings with robust construction, higher load capacity, and suitable material properties should be chosen to ensure longevity and reliable performance.
2.Heat Generation:
Challenge: The compression process in screw compressors generates heat, which can lead to elevated bearing temperatures and potentially compromise bearing performance.
Solution: Effective cooling and lubrication systems are essential to manage heat generation. This includes maintaining proper oil flow and using coolants to dissipate heat. Monitoring bearing temperatures and implementing temperature alarms can help prevent overheating.
3.Lubrication:
Challenge: Inadequate or incorrect lubrication can result in premature bearing failure and increased friction.
Solution: Ensure proper lubrication by using the manufacturer-recommended lubricants and adhering to scheduled maintenance intervals. Regularly check oil quality and levels, and maintain a reliable lubrication system to guarantee optimal bearing performance.
4.Contaminants:
Challenge: Dust, debris, and other contaminants can infiltrate the compressor, potentially causing abrasive wear and corrosion in the bearings.
Solution: Employ effective filtration systems to prevent contaminants from entering the compressor. Additionally, use high-quality seals and shields to protect bearings from external contaminants and maintain a clean operating environment.
5.Vibration:
Challenge: Excessive vibration can lead to premature bearing wear and negatively impact overall compressor efficiency.
Solution: Implement routine vibration analysis to detect and diagnose vibration-related issues. Correct any misalignment or imbalance problems promptly. Balancing rotating components and employing vibration-damping materials can further address this challenge.
6.Misalignment:
Challenge: Poor alignment of screw compressor elements can result in uneven loading on bearings, accelerating wear and reducing their service life.
Solution: Conduct regular alignment checks and adjustments to ensure that the compressor elements are correctly aligned. Proper alignment not only prolongs bearing life but also enhances compressor efficiency.
7.Corrosion:
Challenge: In environments with high humidity or corrosive gases, bearing corrosion can compromise their integrity and performance.
Solution: Select bearings made from corrosion-resistant materials or apply protective coatings to shield them from corrosive elements. Regular inspections and corrosion prevention measures are also essential.
8.Fatigue and Fracture:
Challenge: Repeated cycles of loading and unloading, common in screw compressors, can lead to bearing fatigue and eventual fracture.
Solution: Monitor bearing life expectancy and replace bearings according to a proactive maintenance schedule. Implementing bearing condition monitoring systems can provide early warnings of potential issues.
9.Overheating:
Challenge: Overheating due to excessive friction or inadequate cooling can cause bearings to fail prematurely.
Solution: Perform regular maintenance checks to ensure proper lubrication and cooling system functionality. Employ efficient cooling methods and monitor bearing temperatures to prevent overheating.
10.Inadequate Maintenance:
Challenge: Neglecting regular maintenance and monitoring can lead to unexpected bearing failures, resulting in costly downtime.
Solution: Establish a comprehensive maintenance program, including routine inspections, lubrication checks, and condition monitoring. Implementing predictive maintenance techniques can help identify issues before they escalate.
11.Bearings with Seals:
Challenge: Some screw compressors incorporate bearings with integrated seals, and if these seals fail, it can lead to contamination and reduced bearing life.
Solution: Regularly inspect integrated seals and replace damaged or worn seals promptly. Implementing redundant sealing systems can add an extra layer of protection against contaminants.
13.Start-Stop Cycling:
Challenge: Frequent start-stop cycles can wear out bearings more rapidly.
Solution: To mitigate the impact of frequent cycling, consider using soft start mechanisms or variable speed drives. These technologies reduce the stress on bearings during startup and shutdown.
Screw Compressor Thrust Spherical Roller Bearings
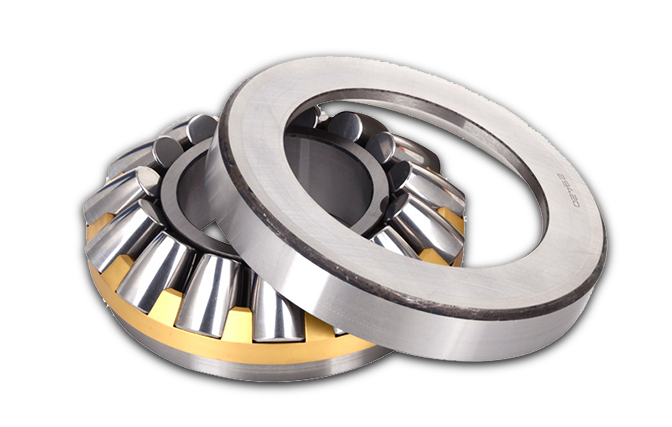
DHK thrust self-aligning roller bearings are available in three different configurations based on different dimensions and cage designs.
Small and medium size self-aligning roller bearings can be solid copper cage (suffix MB) or stamped steel cage (suffix J);
The standard structure for large self-aligning roller bearings is a solid copper cage (suffix MB).