Common failure modes of screw compressor bearings include:
1.Fatigue Failure:
Description: Fatigue failure in screw compressor bearings results from repeated cyclic stresses, which cause microcracks to develop and propagate, eventually leading to catastrophic failure.
Prevention/Mitigation: Ensure proper bearing selection based on load conditions and operating speeds. Maintain appropriate lubrication and viscosity to reduce friction and wear. Implement routine inspections to identify early signs of fatigue, such as surface pitting or spalling. Consider upgrading to bearings with higher fatigue resistance if necessary.
2.Overheating:
Description: Overheating occurs when excessive friction or inadequate cooling mechanisms lead to elevated temperatures in the bearing. This can result in lubricant breakdown and reduced bearing life.
Prevention/Mitigation: Regularly monitor and control operating temperatures. Ensure proper lubrication by using the correct type and amount of lubricant. Address issues like misalignment, overloading, or inadequate cooling promptly. Implement temperature sensors and alarms for early detection of overheating.
3.Contamination:
Description: Contamination of the bearing interior with particles, dirt, or moisture accelerates wear and reduces bearing lifespan.
Prevention/Mitigation: Install effective seals and filtration systems to prevent foreign particle ingress. Maintain a clean environment around the compressor. Perform regular inspections and cleaning of bearing housings to remove contaminants. Use proper lubricants to resist contamination.
4.Misalignment:
Description: Misalignment occurs when the bearing is not properly aligned with the rotor, leading to uneven loading and accelerated wear.
Prevention/Mitigation: Conduct precise alignment during installation and periodically thereafter. Implement laser alignment tools to ensure accurate alignment. Regularly monitor alignment and make adjustments as needed to distribute loads evenly across the bearing.
5.Inadequate Lubrication:
Description: Inadequate lubrication results in increased friction, heat, and wear within the bearing.
Prevention/Mitigation: Establish a stringent lubrication schedule, using the manufacturer's recommended lubricants and quantities. Monitor lubricant quality and cleanliness regularly. Implement automatic lubrication systems for consistency.
6.Corrosion:
Description: Corrosion can occur when bearings are exposed to moisture or corrosive substances, leading to pitting and surface damage.
Prevention/Mitigation: Use corrosion-resistant materials for bearing components. Maintain a dry environment around the compressor and protect against chemical exposure. Implement regular inspections and corrosion prevention measures, such as coatings or protective barriers.
7.Excessive Load:
Description: Subjecting bearings to loads beyond their design capacity can cause premature failure.
Prevention/Mitigation: Adhere to manufacturer's load limits and operating guidelines. Avoid abrupt load changes and overloading. Consider upgrading to higher-capacity bearings if required.
8.Bearing Fatigue:
Description: Bearing fatigue can occur in high-cycle applications, causing fatigue cracks and eventual failure.
Prevention/Mitigation: Choose bearings with higher fatigue life ratings for applications with frequent start-stop cycles. Implement load distribution mechanisms to reduce localized stresses. Consider vibration monitoring to detect early signs of fatigue-related issues.
9.Vibration and Shock:
Description: Excessive vibration and shock loads can lead to premature bearing wear and damage.
Prevention/Mitigation: Implement vibration monitoring systems to detect abnormal vibration levels. Use shock absorbers or dampeners to reduce the impact of shocks. Regularly maintain and replace worn components contributing to vibration.
10.Inadequate Installation:
Description: Improper installation practices, such as incorrect torque values or damaged components, can lead to bearing failure.
Prevention/Mitigation: Follow manufacturer-recommended installation procedures meticulously. Use calibrated tools and skilled technicians for installation. Conduct post-installation inspections to ensure proper assembly and torque values.
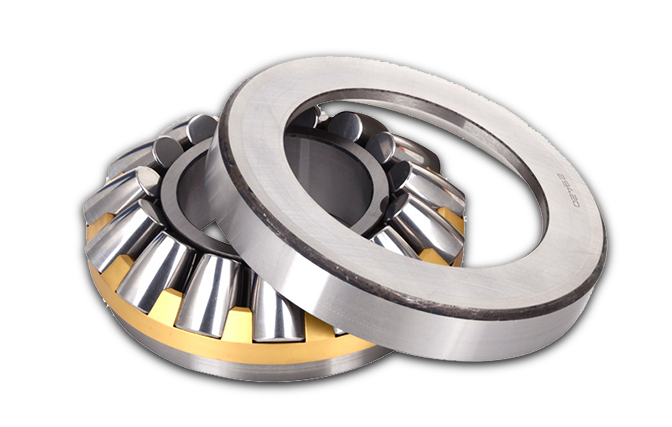
Thrust spherical roller bearings are the same as spherical roller bearings. The raceway surface of the race is a spherical surface centered on the same point on the central axis of the bearing.