Determining the appropriate interval for screw compressor bearing replacement involves a combination of factors, including operating conditions, maintenance history, and performance monitoring. Here's a systematic approach:
Operating Conditions: The operating environment of a screw compressor can vary widely depending on factors such as industry, application, geographic location, and ambient conditions. Compressors used in offshore oil and gas platforms face different challenges compared to those operating in industrial facilities or manufacturing plants. Analyzing the nuances of the operating conditions allows maintenance personnel to identify potential stressors that may accelerate bearing wear, such as exposure to corrosive gases, high humidity levels, or frequent starts and stops. By quantifying these factors and their impact on bearing performance, users can tailor their maintenance approach to address specific challenges effectively.
Maintenance History: A thorough review of the maintenance history provides valuable insights into the performance trends of screw compressor bearings over time. It enables users to identify patterns of failure, recurring issues, or unexpected deviations from expected performance metrics. Analyzing historical data allows maintenance teams to correlate maintenance activities with equipment reliability and uptime, identifying areas for improvement and optimization. By leveraging historical maintenance records, users can develop proactive strategies for mitigating known risks, improving maintenance practices, and extending the lifespan of critical components such as bearings.
Performance Monitoring: Performance monitoring is not limited to periodic assessments but encompasses continuous real-time monitoring of key operational parameters. For instance, modern screw compressor systems are equipped with sensors and monitoring devices that provide a wealth of data on variables such as vibration levels, temperature gradients, pressure fluctuations, and energy consumption. By leveraging advanced monitoring technologies and data analytics tools, users can detect subtle changes in bearing behavior that may signal impending failure. Real-time performance monitoring enables proactive decision-making, allowing maintenance teams to intervene before issues escalate and impact production.
Condition Monitoring: Condition monitoring goes beyond traditional maintenance approaches by focusing on early detection of abnormal operating conditions and incipient failure modes. It involves deploying a suite of diagnostic techniques, including vibration analysis, oil analysis, thermography, ultrasonic testing, and acoustic emissions monitoring. These techniques enable maintenance personnel to assess the health of screw compressor bearings non-invasively and identify potential issues before they manifest as catastrophic failures. By integrating condition monitoring into routine maintenance practices, users can minimize unplanned downtime, optimize maintenance schedules, and maximize equipment reliability.
Risk Assessment: Risk assessment is a systematic process for evaluating the likelihood and consequences of potential failure scenarios associated with screw compressor bearings. It involves identifying hazards, assessing risks, prioritizing mitigation measures, and developing contingency plans. Factors such as the criticality of the equipment, the impact of failure on production processes, regulatory compliance requirements, and safety considerations are all taken into account during the risk assessment process. By quantifying risks and their potential consequences, users can allocate resources effectively, prioritize maintenance activities, and implement targeted interventions to reduce the likelihood of bearing-related failures.
Screw Compressor Thrust Spherical Roller Bearings
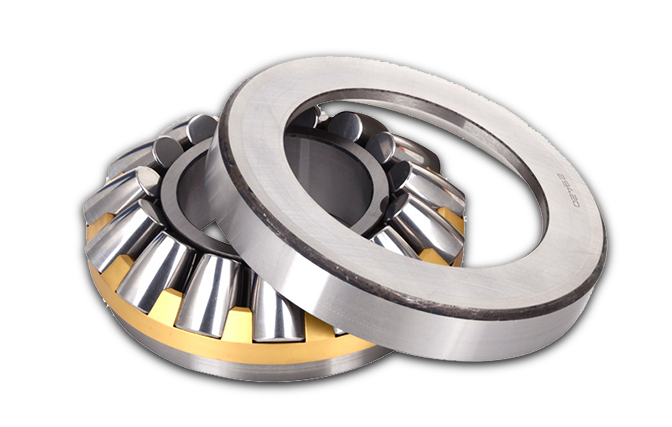
Screw Compressor Thrust Spherical Roller Bearings
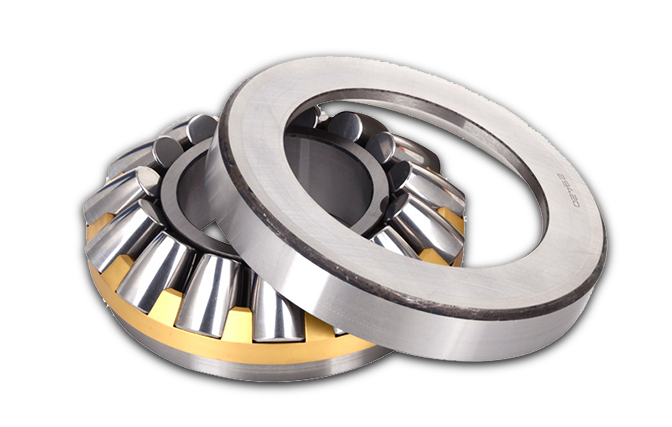
DHK thrust self-aligning roller bearings are available in three different configurations based on different dimensions and cage designs.
Small and medium size self-aligning roller bearings can be solid copper cage (suffix MB) or stamped steel cage (suffix J);
The standard structure for large self-aligning roller bearings is a solid copper cage (suffix MB).