Balancing the rotor in a screw compressor is a critical process that ensures smooth operation, reduces vibrations, and prolongs the life of bearings and other components. Here's an overview of the balancing process and its impact on bearing life:
Balancing Process of the Rotor:
1.Static Balancing:
Measurement: The rotor's weight distribution is measured statically while it's stationary.
Adjustment: Counterweights are added or removed to balance the rotor statically. This ensures that the center of mass is at the rotor's axis of rotation.
2.Dynamic Balancing:
Measurement: The rotor is spun at operating speed, and dynamic measurements identify unbalance.
Adjustment: Small trial weights are added or removed at specific locations until the rotor operates without significant vibrations. High-speed balancing machines are often used for precision.
Impact on Bearing Life:
1. Reduced Vibrations:
Impact: Balanced rotors significantly reduce dynamic and static vibrations, thereby mitigating the risk of imbalance-induced resonance and ensuring smooth operation of the screw compressor.
Effect: By minimizing vibrations, bearings are subjected to less stress and fatigue. This results in reduced wear and tear, enhancing the operational longevity of the bearings and the entire screw compressor system.
2. Minimized Radial Loads:
Impact: Unbalanced rotors generate radial loads on bearings, causing uneven pressure distribution.
Effect: Balancing the rotor minimizes these radial loads, ensuring that bearings experience uniform pressure. This uniformity prevents localized wear and extends bearing life by maintaining optimal load distribution across bearing surfaces.
3. Enhanced Lubrication:
Impact: Vibrations can disrupt the lubricant film between bearing surfaces, leading to increased friction and heat generation.
Effect: Balanced rotors reduce vibrations, ensuring consistent lubrication between bearing elements. This stable lubrication minimizes wear, prevents metal-to-metal contact, and preserves the integrity of the bearings, resulting in extended operational life.
4. Prevention of Resonance:
Impact: Unbalanced components can trigger resonance, causing severe mechanical failures and downtime.
Effect: Proper rotor balancing eliminates the risk of resonance-related issues. Bearings remain stable, avoiding excessive forces that could lead to catastrophic failures, ensuring uninterrupted operation and reducing costly downtime.
5. Improved Reliability:
Impact: Balanced rotors enhance the overall reliability and operational stability of the screw compressor system.
Effect: Bearings experience reduced strain and fatigue, leading to increased reliability. The system operates consistently, minimizing the likelihood of unexpected breakdowns. This reliability ensures continuous productivity and reduces maintenance efforts and costs.
6. Energy Efficiency:
Impact: Vibrations and unbalanced components increase energy consumption due to higher resistance and mechanical losses.
Effect: Balanced rotors optimize energy efficiency by reducing resistance and losses within the system. Bearings experience less stress, resulting in smoother operation and lower energy consumption. This energy efficiency not only lowers operational costs but also contributes to environmental sustainability.
The meticulous balancing of the rotor in a screw compressor is pivotal in ensuring optimal performance, reliability, and longevity of bearings. By addressing issues related to vibrations, load distribution, lubrication, resonance, reliability, and energy efficiency, balanced rotors significantly enhance the operational efficiency and cost-effectiveness of the entire screw compressor system.
The meticulous balancing of the rotor in a screw compressor is pivotal in ensuring optimal performance, reliability, and longevity of bearings. By addressing issues related to vibrations, load distribution, lubrication, resonance, reliability, and energy efficiency, balanced rotors significantly enhance the operational efficiency and cost-effectiveness of the entire screw compressor system.
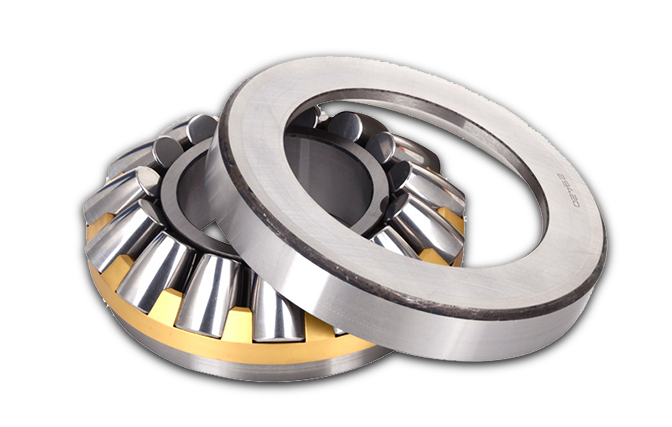
Thrust spherical roller bearings are the same as spherical roller bearings. The raceway surface of the race is a spherical surface centered on the same point on the central axis of the bearing.