Several lubrication methods are commonly used for machine tool bearings to ensure smooth operation and extend their lifespan. These methods include:
1.Grease Lubrication:
Grease is a viscous lubricant that consists of a base oil blended with a thickening agent such as a soap. This combination gives grease its semi-solid consistency, allowing it to stay in place and adhere to bearing surfaces effectively. Grease offers several benefits in machine tool applications:
Sealing: Grease forms a protective barrier that seals out contaminants like dirt and moisture, preventing them from reaching the bearing surfaces.
Longevity: Due to its consistency, grease tends to have a longer effective lubrication life than oil, making it suitable for applications where regular maintenance is not feasible.
Simplicity: Grease application is relatively simple, often requiring just periodic regreasing to maintain lubrication.
2.Oil Lubrication:
Oil lubrication involves the use of liquid oils to provide lubrication to bearing components. Different methods of oil lubrication cater to various operational demands:
Oil Bath Lubrication: Bearings are partially immersed in a reservoir of oil. As they rotate, they pick up a film of oil that adheres to the surfaces, ensuring continuous lubrication.
Oil Mist Lubrication: Oil is atomized into fine mist particles using a dedicated system. This mist is then directed toward the bearing surfaces, providing lubrication while also carrying away heat generated by friction.
Oil Jet Lubrication: Precise jets of oil are directed onto specific bearing points. This targeted approach ensures effective lubrication while minimizing wastage of lubricant.
3.Air-Oil Lubrication:
Air-oil lubrication combines compressed air and oil to create a mist that is delivered to the bearings. The benefits of this method include:
Cooling: The air helps in cooling the bearings, making it suitable for high-speed applications where heat generation is a concern.
Lubrication Efficiency: The mist effectively reaches the bearing surfaces, ensuring consistent lubrication even in challenging environments.
4.Oil Circulation Lubrication:
This method involves a closed-loop system where oil is continuously circulated through the bearings. Additional features of oil circulation
lubrication include:
Filtration: The oil is passed through filters to remove contaminants, ensuring the lubricant's cleanliness and preventing abrasive particles from damaging bearing surfaces.
Cooling: The oil is often directed through coolers to manage the temperature and maintain optimal operating conditions.
5.Solid Lubrication:
Solid lubricants, like graphite or MoS2, offer unique advantages in certain applications:
Extreme Conditions: Solid lubricants can withstand high temperatures, vacuum environments, and radiation exposure, making them suitable for specialized applications such as aerospace and vacuum chambers.
Low Friction: These materials have inherent low-friction properties, reducing wear and extending bearing life.
Each lubrication method has its own advantages and considerations. Proper lubrication is essential for reducing friction, preventing wear, dissipating heat, and ensuring the longevity and optimal performance of machine tool bearings.
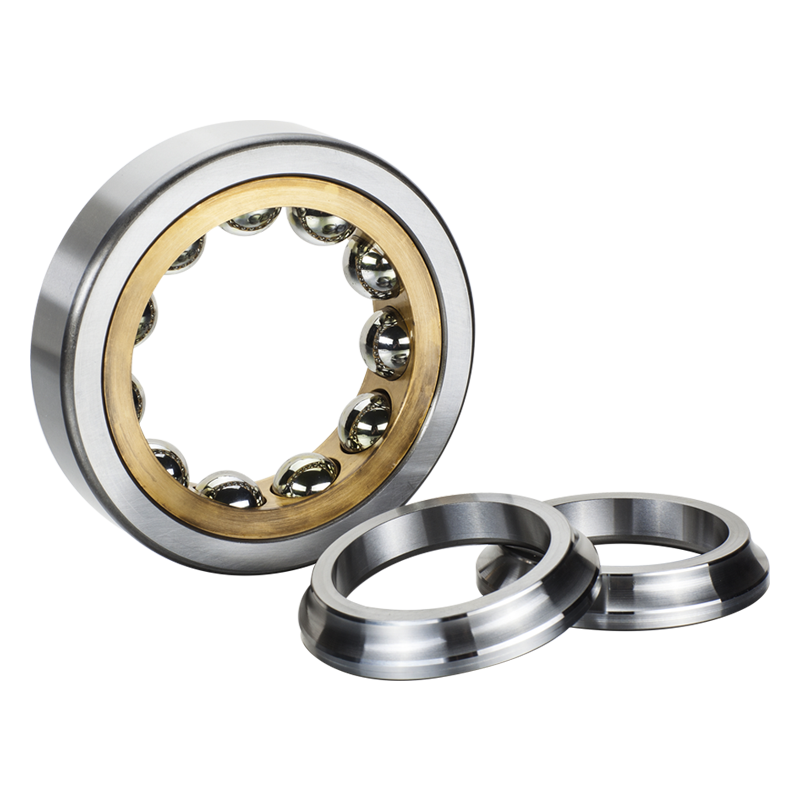
Four Point Contact Ball Bearings are a specialized type of angular contact ball bearings. They are designed to handle combined loads, including radial and axial forces, in a single bearing unit. Unlike traditional ball bearings that predominantly support radial loads, 4-point bearings have a distinctive design that allows them to accommodate both types of loads simultaneously.